Located at our Davenport facility on the bluffs above Highway 1, just north of Davenport, our sawmill has occupied the same location since 1964. Here, redwood logs harvested by our forestry department are processed into a variety of lumber dimensions and grades. Wood scrap that is not turned into lumber gets chipped and ground into sawdust mixes and mulch, so that none of the wood fiber that enters the sawmill goes to waste.
Big Creek Lumber’s sawmill is one of the few remaining operational sawmills in California, and is the only Redwood sawmill on the Central Coast.
From Log to Lumber
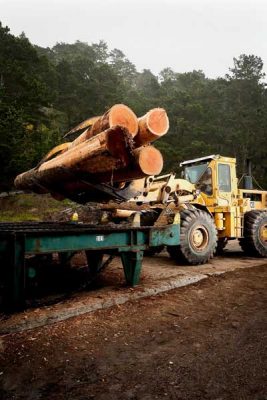
Before entering the sawmill, de-barked logs are transferred from the log deck to the mill site with a CAT 950 log loader where the logs are then placed onto the live deck. It is both the loader operator and live deck operators’ responsibility to keep the sawyers well supplied with the right mix of logs so that production flows as smoothly as possible. The proper mix of log sizes entering the sawmill can greatly increase efficiency of production through the mill. From the live deck, logs move to either the pony rig band saw or the head rig band saw, depending on size. The pony rig is a smaller version of the head rig and is primarily used to “break down” smaller, more uniform logs. All other logs, up to 6 feet in diameter, are processed through the head rig. In both the head rig and the pony rig, full logs are cut down into “flitches” or “cants” which are generally 10-56 inches wide and of varying lengths with rough, uneven edges. The term “flitch” is typically used to describe pieces up to 4 inches thick, while the word “cant” describes anything thicker than 4 inches. The head rig is made up of a carriage that moves the log through and away from a 43-foot long, 11-inch wide band saw on a 7-foot diameter band wheel. The operator, or “sawyer”, who controls the rig, sits in a small, protected booth directly behind the band saw. It takes years to become proficient in the skills needed to be an excellent sawyer. The sawyer must assess each log as he rapidly rolls it onto the carriage to position it so it yields the highest value lumber possible. The head rig is equipped with a green laser line projector so the sawyer can see where the cut will be made and determine the best cut setting to maximize recovery of quality and volume from each log. Each log is unique and the sawyer must carefully reevaluate the log being sawn with each pass of the carriage. This all must occur with speed, dexterity and caution. Mistakes made while operating the rig can both damage equipment and be dangerous. In the old days, 2 or 3 operators would ride the carriage back and forth past the saw on what was called “a long ride to nowhere”.
From the pony rig and the head rig, the flitches and cants move via transfer chains to the edger to be processed even further into individual boards of various widths. The edger contains a group of shifting circular saws that can be selected by the “edgerman” to cut each flitch or cant to various widths. Five laser light beams assist the edgerman to carefully make adjustments to the edger’s saws and to the alignment of the flitch as it enters the edger. The edgerman must have excellent lumber grading skills and a good understanding of the relative value of each lumber grade and dimension so he can consistently make the choices necessary to minimize waste and recover the maximum value from the flitches and cants.
From the edger, boards move to a transfer table that transports them to the trim saw. Spotters help move lumber away from the edger and straighten and space the pieces so the drop sorter operator can sort the waste from the usable lumber and so lumber flows smoothly towards the trim saw. At the trim saw, the “trimmerman” determines to which length the boards will be cut to maximize their value, and inputs a series of commands to a computer that controls when the trim saw will lower and cut the boards to length. Ends are trimmed square and often a piece is trimmed shorter to eliminate a defect that would not be allowed in its predominant grade of lumber. Others are trimmed into two pieces, one portion that will make a more valuable grade and another that falls into a lower grade. The trimmerman must have excellent concentration, good dexterity and a solid knowledge of lumber grade and relative value. Much value can be gained or lost at the trim saw. Waste material from the trim saw falls through a drop gate to the outside slasher conveyor and, along with sawdust and other scrap material, is fed into a processing facility that chips and pulverizes it into premium quality soil mulch. No wood fiber goes to waste in the mill.
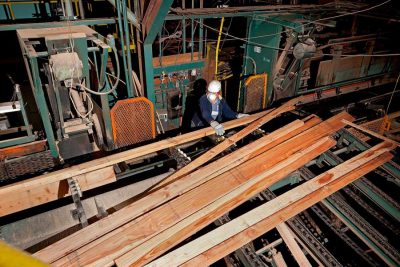
Boards from the trim saw are fed onto the grading table, where a series of highly skilled lumber graders accurately and rapidly assess each board to determine which grade it falls within and then mark it accordingly with an identifying mark. A good grader can determine if a board will gain value if it is re-sawn to a different dimension or trimmed to a different length. A grader must be so familiar with the grade specifications that an accurate decision can be made almost instantly.
After grading, boards either exit the sawmill on the green chain, or are diverted back to be re-sawn or re-trimmed. The re-saw is used to rip a board to different dimensions in order to maximize its value or to improve the consistency of size. By re-trimming a board to different lengths, overall value can often be increased.

On the green chain outside the sawmill, lumber is pulled and sorted into stacks by grade and dimension. The stacks are tallied and taken away for storage until lumber of specific grades and dimensions is needed. The “green chain pullers” must be careful that each grade and dimension is properly sorted. Mistakes can be costly or can result in an inferior product. A good chain puller is able to spot errors that occur inside the mill. Many sawmill employees start out working in this position. As they learn to recognize which defects are permitted in each lumber grade, they have the opportunity to move to other positions within the sawmill.
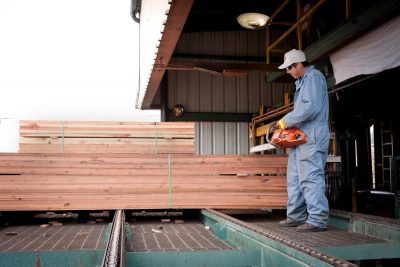
Lumber undergoes final processing in the planing mill, where the edges and faces of the boards are surfaced. Typical surfacing configurations include Rough (no sides surfaced), S1S2E (surfaced one side and two edges) and S4S (surfaced four sides). Some boards may be re-sawn or re-trimmed into fence boards with either plain tops or dog-ears.
Additional employees occupy crucial support functions to the sawmill. Millwrights and electricians are responsible for keeping the mill running throughout production time. They “chase whistles” or calls for help from the various operators when adjustments or repairs are needed. The goal of every sawmill is to have as little costly “down time” as possible. Production time repairs are often quick fixes and additional maintenance is required after the shift is completed or on weekends. Many of the operators perform the routine greasing and maintenance on the machine they operate. A good saw filer is critical to the safety, speed and accuracy of the milling process. They are truly artists at their work which includes the precise grinding of saw teeth, re-tipping, benching and leveling the saws.
For more visit our wholesale redwood lumber products page or our Reseller department.
Sawmill Tours
Big Creek Lumber often offers sawmill tours for educational groups and participates in educational programs in conjunction with the California Forestry Challenge, Cal Poly San Luis Obispo, Leadership Santa Cruz County and multiple forestry and agricultural programs. If you are interested in setting up a tour, contact Bob Berlage for additional information.